R&D and application
Details:
(1) New material technology
No. |
Project name |
R&D content |
Source of technology |
Corresponding patent name |
1 |
Electrical frame material—FJ001 aluminum alloy material customization technology | At present, it is a common trend in the electrical industry to process aluminum materials into frames for the decoration of electrical frames, and then meet the needs of various types of products through anodizing, coloring and other processes. Strong, corrosion-resistant, fast heat dissipation, green and environmentally friendly and easy to recycle, it is deeply welcomed by downstream brand home appliances. With the increasingly fierce market competition, downstream deep processing has higher and higher requirements on the appearance and quality of blank materials, which puts forward higher requirements for upstream raw materials. In order to meet the requirements of the plasticity of the extruded product, the customized shape and color of the customer, it is necessary to adjust the material composition to meet the individual needs of the market. |
Independent research and development |
-- |
2 |
Formation mechanism and solution technology of coarse grains in reverse extrusion of 5056 aluminum alloy | 5056 aluminum extrusion products are prone to coarse crystals and difficult to control during the reverse extrusion production process, especially when the extrusion ratio exceeds 40 (cross-sectional area / holding material area) or thin-walled seamless aluminum tubes, it is necessary to increase The temperature of the extrusion rod can only meet the production requirements under the condition of 520-530℃. The products produced under such process conditions will have obvious recrystallization and coarsening after anodization, and the coarse low-magnification grain structure will appear, which will affect the final appearance and texture, resulting in poor finished products. The company has perfected the prevention and solutions in the production process by studying the formation mechanism of the coarse grains of the low-magnification structure of the 5056 aluminum material. |
Independent research and development |
-- |
3 |
A high-gloss FJ002 aluminum alloy material technology | With the improvement of public aesthetics, the end consumer market has higher and higher requirements for the performance, appearance and texture that aluminum alloy processing needs to meet. Industrial electronics, home appliances and other industries use aluminum alloys to be easily oxidized and colored, easy to spray, polish, and wire to meet downstream customers. With the competitive trend in the market industry, the demand for differentiated competition is becoming more and more obvious, and the requirements of customers are getting higher and higher. Aluminum alloy polishing products are used in more and more frame materials and decorative shells. The requirements for raw materials such as degree and impurities are relatively high. The development of aluminum alloy raw materials for polished products, the improvement of yield and efficiency, etc., constitute an important part of product competitiveness. |
Independent research and development |
-- |
4 |
A flexible FJ003 aluminum alloy material technology suitable for bending | The purpose of this research is to provide an aluminum alloy material used in bending products. Through the regulation of the main Si and Mg contents of the aluminum alloy, it is used to control the Mg₂Si content and the process parameters and aging conditions in the extrusion process, so as to improve its material. ductility, toughness and maintain a certain strength. It is conducive to the bending and stamping of extruded materials, reducing the occurrence of fractures and cracks in the bending and forming process, and solving the problem of too narrow seamless width, so as to meet the individual needs of customers and solve the problem of aluminum alloy bending. |
Independent research and development |
-- |
(2) Mold forming technology
No. |
Project name |
R&D content |
Source of technology |
Corresponding patent name |
1 |
High-efficiency and high-precision mold forming technology | For cylindrical and other material-thickness stretched products, the traditional molding method is to produce on multiple sets of equipment through multiple sets of molds. The company's independent research and development integrates continuous stretching and side punching on a set of automatic continuous molds, which solves the positioning error caused by punching in multiple processes. Greatly reduces, greatly improves production efficiency and product accuracy, and also enhances product competitiveness. |
Independent research and development |
A continuous die stretching device ZL201520978344.X |
2 |
Rotary punching technology | Aiming at the repetitive hole characteristics on the rotary product, for example, high-end speakers will be designed into a cone-shaped cylinder with sound holes all around. The forming method of the holes directly affects the cost, quality and processing efficiency of the product. The company drives the mold core to rotate through the independent research and development servo motor, the material is mounted on the mold core, rotates with the frequency of the punch, and is equipped with sensors and positioning pins with a precision of 0.01mm. This molding method reduces the risk of accumulating tolerances. Low cost, high efficiency, saves a lot of punching equipment (die) or drilling equipment, and has been used for rotary body punching in batches. |
Independent research and development |
A servo motor rotary stamping die ZL202120374001.8 |
3 |
Large-scale high-precision stamping die technology | At present, the frame of high-end TV sets is mostly made of aluminum metal material, and then surface treatment is used for decoration. The original traditional frame is changed from four pieces into one piece, and the processing and forming method of the one-piece frame is related to the cost and production efficiency of the frame. The self-developed super-long mold (4 meters) for straight material processing before frame bending is completed by one punching, saving a lot of equipment required for traditional CNC processing and forming, the efficiency is increased by about 10 times, and the product processing cost is reduced by about 50%. The precision reaches 0.05mm, and it has been used for stamping and forming of metal integrated frame of TV in large quantities, which has produced good economic benefits. |
Independent research and development |
A stamping method 202111060446.X is under substantive examination of invention patent; A stamping die ZL202122197122.2 |
4 |
The key technology of TV seamless bending intelligent manufacturing process | In the occasions where the frame of TV/monitor/advertising machine has required strength, most of the integrated frame adopts seamless bending. The seamless bending frame not only effectively protects the screen but also reinforces the whole machine. The company's independent research and development of the company's independent research and development of aluminum frame seamless bending device and bending method, the A side of the frame can be seamless up to 17mm, and the number of products in the same industry is only about 12mm, and it solves the irregular plastic deformation during the bending process. The device and method are in a leading position in the industry, and have a solid technical foundation for the internal reserve. |
Independent research and development |
A seamless bending device and bending method 2021109859472 (in the process of invention patent examination); a seamless bending device ZL202122038745.5 |
5 |
Study on Forming Technology of Irregular Dense Holes | Inconsistent size and irregular arrangement of dense hole forming, such as using high-speed drilling machine to frequently change tool specifications, resulting in low efficiency and high processing costs. Due to the irregular arrangement of holes, the continuous die is used for stamping and forming, the cost of the die is high and the equipment requirements are high. The traditional method is to punch several sets of mold bases on several punching machines. Through independent research and development, the company designs a stamping die for the forming of such holes, and puts all the holes on a set of die for stamping. Each time the numerical control moves a certain part, it can be replaced to make different punches work in batches. The product is fixed, and holes of different specifications can be continuously punched, which can not only solve the problem of non-dropping during punching, but also avoid the concentration of punching force, which will cause the mold to be easily damaged and the punching force needs to use large tonnage equipment. |
Independent research and development |
-- |
6 |
Surface coating thin metal material drawing technology | The surface appearance of traditional electrical structural parts is usually formed by various processing methods and then various coloring treatments are applied to the surface. This forming method is suitable for products with certain strength and relatively large spot size. Today's various electrical and electronic products pursue the trend of being light and thin, and the supporting structural appearance parts should also be designed to be light, thin and small in size to meet the requirements. However, the appearance of these structural parts is treated by the aforementioned forming method, because the shape of the processing process will be greatly deformed, so it is impossible to Get a good appearance. The company researches and develops the molding process, which uses the coated large plate to drop the small material and then stretches it. The self-developed stretching die uses 0.15mm thick coating material. The product is 1,565mm long, 5.5mm wide and 6.5mm high, and the inner R angle is The sharp corners have been successfully developed and mass-produced. Not only does the coating not fall off, but also the straightness can be guaranteed within 0.1mm, which not only meets the needs of customers but also produces good economic benefits. |
Independent research and development |
-- |
7 |
Curved TV Frame Application Technology | The difficulty in manufacturing a curved TV is to control the rebound of plastic deformation. The amount of rebound of different sections of extrusion is different. The empirical formula is difficult to calculate. Only molds with different curvatures can be manufactured for testing. The mold is added to fill the buffer material, and the compensation pressure is added at the stress release point of the camber structure. |
Independent research and development |
A seamless curved bending machine and the TV frame produced therefrom ZL201920369385.7 |
(3) Surface treatment technology
No. |
Project name |
R&D content |
Source of technology |
Corresponding patent name |
1 |
Four-color oxidation technology | Multi-color oxidation is a combination of multiple oxidation treatments on the same product, which can enrich the surface effect and present colorful aesthetics. The company realizes the control of the thickness of the oxide film of different orders by adjusting the voltage value of the non-stop order, the oxidation power-on time, and the temperature of the oxidation bath, so as to ensure the bonding force of the oxide film. shedding conditions. |
Independent research and development |
Four-color oxidation process CN201810670086.7 (application) |
2 |
Wet environmental protection automatic polishing technology | Surface polishing is a common process for aluminum alloy surface treatment. The purpose is to increase the surface brightness and metal texture of the product. Polishing dust is usually generated during the process. In response to the needs of a major domestic customer, the company developed a wet environmental protection polishing technology that does not generate dust at all. By adjusting the proportion of the customized polishing liquid and the adjustment of the polishing wheel pressure, the requirements of different brightness of the product surface are realized, and the whole process is environmentally friendly. |
Independent research and development |
A wet-type environmental protection three-stage automatic mirror polishing device ZL202020137557.0 |
3 |
Continuous batch tooth highlight technology | Pyramid modeling refers to the technology of modeling and processing the surface of aluminum alloy products after oxidation treatment. The company uses Jingdiao professional equipment, special cutter heads and diamond cutters to cut the products. During the process, the cutters rotate at high speed along the program path pre-programmed by special software to produce cutting action, and the surface of the processed products produces a pyramid shape. Through the refraction of light, the surrounding diamond edges are smooth and bright, and the three-dimensional effect of convex and concave is strong, which greatly improves the decorative effect. |
Independent research and development |
A TV frame continuous batch tooth highlight device ZL201820400759.2 |
4 |
Multi-sided grinding wire drawing production line technology | Surface grinding and wire drawing treatment is to form lines on the surface of the workpiece by grinding the product, which has a decorative effect. By analyzing and showing the surface characteristics of the frame-like frame, the company has developed an integrated equipment for grinding and wire drawing, combining four processes of grinding both sides and drawing both sides into one process; through the optimization of the selection of grinding and drawing consumables and the control of the contact pressure between the consumables and the product , The running speed of the automatic conveying line, the surface of the product is beautified, so that the surface lines of the product are parallel and clear, and the metal texture is greatly improved. |
Independent research and development |
A grinding and drawing device ZL201820560731.5 |
5 |
Backplane frame drawing and high-gloss comprehensive processing technology | Independent research and development has developed a brushed high-gloss composite machining tool. The tool has a V-shaped flat bottom. The two sides of the V are slightly evenly serrated. While cutting, the surface leaves a uniform density of hair lines. The flat bottom is about 3mm single crystal diamond edge, at 20,000 The high-gloss surface can reach T=0.4 at the speed of rpm/min. This technology overcomes the problem of scratching the high-gloss when the multi-edge processing is performed and the scrap pin hangs. Two kinds of surface treatment effects with different textures are achieved, and the highlight width error is within 0.05mm. |
Independent research and development |
A high-gloss drawing comprehensive processing device ZL202120373977.3 |
6 |
Manipulator flexible intelligent control grinding and wire drawing technology | At present, for U-frame products in the same industry, the general wire drawing process is to unfold the long material, bend it into a U frame, and then manually repair the wire drawing pattern, which has low production efficiency and high defect rate. ”-shaped fixture, the fixture is in the superposition mode of the pyramid, the bottom 100-inch frame is pushed up to the minimum 43-inch frame, the fixture adopts the inner guide column to quickly locate and disassemble, and the end of the manipulator is equipped with an elastic steel brush chuck to follow the product shape Make straight lines evenly. The production efficiency and yield rate are greatly improved. At the same time, the manipulator wire drawing technology solves the limitation of wire drawing on the product form, enriches the wire drawing process, and provides a strong guarantee for the realization of intelligent manufacturing on the production site. |
Independent research and development |
An industrial robot flexible wire drawing device ZL202120373334.9 |
(4) Production technology
No. |
Project name |
R&D content |
Source of technology |
Corresponding patent name |
1 |
Efficient CNC technology | The current traditional single-head single-channel structure 4.5-meter CNC machine is technically upgraded and manufactured, and a spindle, a follow-up tool magazine and a high-speed braking control system are added. The new equipment is a dual-drive dual-channel high-speed drilling and tapping machine. The main advantage of two spindles Relatively independent operation without interfering with each other, the 4.5-meter processing platform is divided into two independent units, which can realize the simultaneous processing of the same 4-meter-long product or two different products on two axes, overcoming the problem of long processing time with ordinary single heads and greatly improving efficiency. At the same time, the accuracy of the equipment is also greatly improved, which can achieve a single positioning accuracy of 0.01mm and a repeat positioning accuracy of 0.005mm. The design of the whole machine structure system is the first in China. |
Independent research and development |
-- |
2 |
Six-axis manipulator automatic film technology | The research is centered on the manipulator, and four sets of special fixtures are set on four sides. The multi-degree-of-freedom of the six-axis manipulator is used to realize complex and high-precision movements. The flexible programming technology realizes multiple varieties and batches, breaking through the limitations of ordinary linear film, especially when the film surface is It is a curved surface. The inconsistency between the pressing force and the holding time will cause the protective film to be out of position and warped. It is suitable for U-shaped frames and curved frames. The application of this technology has played a role in improving quality and efficiency. The precision of the film is mentioned to be 0.2mm , There are no bubbles in the film, and the adhesion meets the 72-hour hot and cold test without warping. The key is to realize automatic filming, improve production efficiency and save costs. |
Independent research and development |
A six-axis manipulator automatic film sticking device ZL202120373905.9 |
3 |
NC Infrared Measuring Flatness Technology | This technology uses a flatness device for fast and effective measurement of ultra-thin backplanes, breaking through the traditional horizontal flat-laying method, placing the backplane in a vertical direction, overcoming the influence of its own weight and gravity, and adding motors and moving shafts in the left, right, up and down directions. The device emits infrared rays to measure the flatness of the backplane. In this process, the flatness of any position of the backplane can be measured. The process is automated and controlled, which can quickly obtain accurate measurement results and improve the overall efficiency. |
Independent research and development |
A numerical control infrared measuring flatness device ZL202020125179.4 |
4 |
Brush type automatic cleaning technology | The technology adopts special grinding brush roller transmission, and provides the following cleaning procedures: feeding - degreasing - washing - weak alkali washing - washing - neutralization - washing - rushing water - drying - drying - discharging, the process requires cleaning The liquid temperature is adjustable in the range of 45-60 °C, and the automatic constant temperature is used. The hot air temperature is adjustable in the range of 70-60 °C, and the working temperature is lower than that of the high-pressure spray cleaning method. The equipment can greatly reduce energy consumption. The upper and lower rollers are used to squeeze and brush the workpiece to effectively clean the oil stains on the front and back of the back plate without leaving oil stains. The cleaning is completed at one time, and there is no need for two cleaning operations on the front and back. The process of extrusion The strength is small, the workpiece will not be deformed, and there is no need to install ultrasonic cleaning equipment. The entire project is energy-saving and environmentally friendly, reducing costs, and cleaning is efficient and clean to meet the surface tension test of the dyne pen 38. |
Independent research and development |
A brush type automatic cleaning device ZL202020127806.8 |
5 |
Curved horizontal high-gloss technology | Corner bright edge highlighting is a common method for high-end metal appearance processing. The more popular one is flat highlighting, while arc (curved surface) bright edge highlighting is limited by factors such as equipment, tooling, and human resources. Vertical machine tool tools are usually used for highlighting in the industry. It is difficult to obtain high-quality highlight effects by taking 3D tracks for processing. Self-developed high-gloss tooling, and the main shaft of the equipment is changed from vertical to horizontal, and the original arc-shaped high-gloss tool follows a plane trajectory, so as to obtain high-quality high-gloss edge effect. Recognition, and the improvement of efficiency and quality have enhanced the market competitiveness of structural parts. |
Independent research and development |
-- |
(5) Automated production and assembly technology
No. |
Project name |
R&D content |
Source of technology |
Corresponding patent name |
1 |
Automatic intelligent detection and identification of stamping technology | Due to the large overall volume and high daily demand for the products of this project, there are three stamping steps in total. If manual work is performed, not only are there many operators and labor costs are high, but also the efficiency is low, the quality is unstable, and the production capacity cannot reach the target. For the above problems, with the efforts of the task force, the robot punching was completed: the robot punching three consecutive punches. The three stamping processes are continuously operated by the manipulator. The original operator has been reduced from 4 people per shift to 2 people per shift. The entire automatic line has been put into use, and the cost of operators has been reduced by half, and the production efficiency has also been improved. At the same time, it also reduces the material turnover time between processes, and the scratches in the transfer between processes are also greatly reduced, and the efficiency is significantly improved. |
Independent research and development |
An automatic stamping device for TV frame ZL202120373907.8 |
2 |
3C product automated assembly system technology | For fast-consumer 3C products such as tablets and voice recorders, the old assembly involves a lot of materials, the entire production line is bulky and the flexibility is too low, and a large number of manual operations are not suitable for pull-type production. The quality is poor, the cost is still high, and the missing process also occurs from time to time. In response to the above problems, a project is established by Independent research and development: flat automatic precision assembly line. Through the precise connection of conveyor belts and manipulators, the products are automatically clamped in each process, and the precise foot capture and positioning of the automatic lens, automatic monitoring, realize automatic flow operation of each process, information collection, and automatic feedback of results. By putting the whole automatic line into use, the number of operators is greatly reduced, the work site is unified and tidy, the efficiency is improved significantly, the quality is stable, the turnover of each process is reduced, the internal consumption is reduced, and the market competitiveness is improved. |
Independent research and development |
-- |
3 |
3C heat dissipation structure automatic production line technology | Various electrical appliances have built-in heat sinks, because they are universal and in high demand, but because they are not external parts, whether there is an advantage in production has a lot to do with efficiency and quality stability. Independent research and development 3C automatic production line for heat dissipation structural parts integrates an automatic production line from aluminum extrusion profile sawing, deburring, stamping, film batching, cleaning, inspection, etc., from material cutting to automatic inspection, automatic seamless connection, and continuous production. The efficiency is increased by about 30%, the labor cost is reduced by about 3 times, and the product competitiveness is greatly improved. The company has gradually established a number of production lines, and similar products can be produced on the same line, which improves economic efficiency. |
Independent research and development |
-- |
Other contents
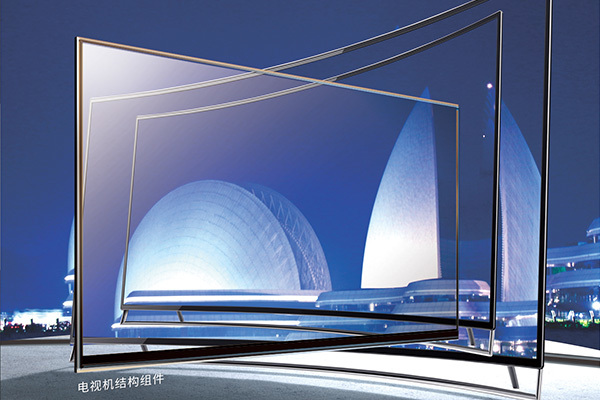
Display terminal precision structural components
Mainly used in smart TVs, educational displays, office displays, e-sports displays, medical displays, fitness displays, and other products. Its main function is to fix the optical module of the display device, serving as one of the key structural materials for the display screen and back panel. It also plays a role in the appearance and personalization of the display device. The internal dimensions and flatness of the product significantly impact the assembly effect of the display screen, helping to improve the overall light leakage and light spot issues of the display device. The flatness and thickness of the product are crucial for the seamless integration of the overall structural material and screen, achieving an immersive viewing experience.
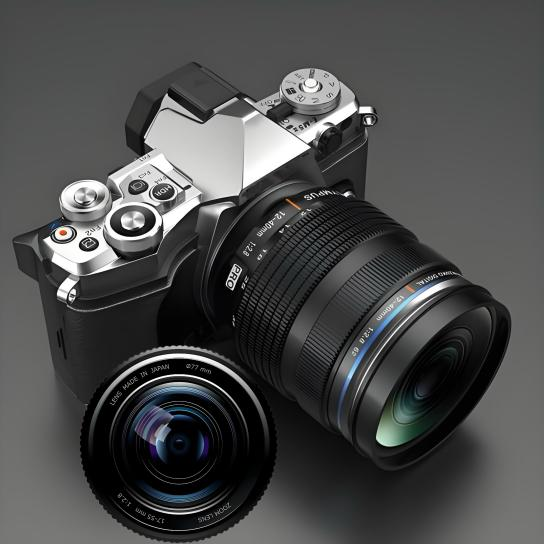
Precision components for digital cameras
Primarily used in the lenses and buttons of digital cameras, this product is a key component that directly impacts image quality. It strictly meets customer requirements for high standards of precision and assembly of precision optical components, and is critical for zoom and focus adjustment. The precision of Fuji Intelligent's products can reach ±0.005mm.
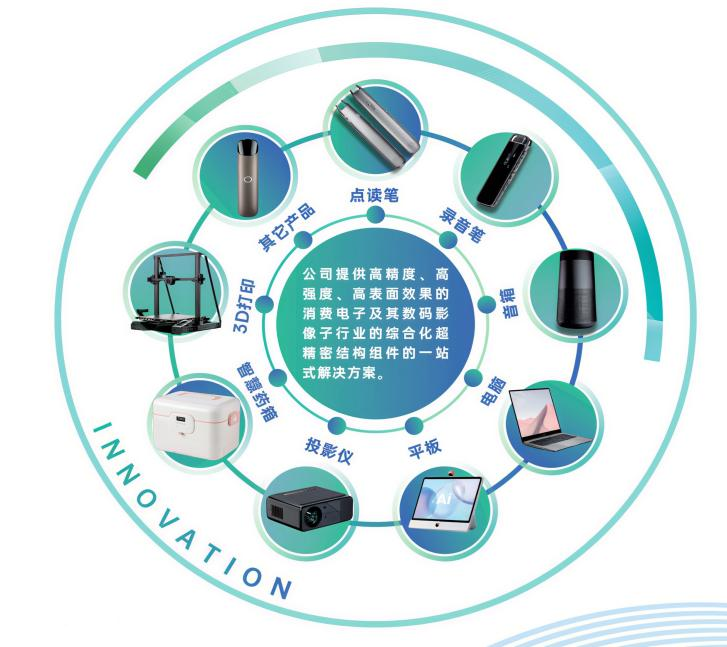
Other precision structural components for consumer electronics
Primarily used in the casings and buttons of recording pens/dictionary pens, educational tablets, and other products. As a key structural material for the device, providing structural support and protecting internal electronic components, the company's advanced processes and surface treatment technology give the product a superior metallic texture and exquisite appearance. The product is lightweight, has high mechanical strength, good stability, and high durability. The perfect combination of plastic and metal enhances the overall appearance, visual effect, and smooth touch of the device, significantly impacting the display effect.
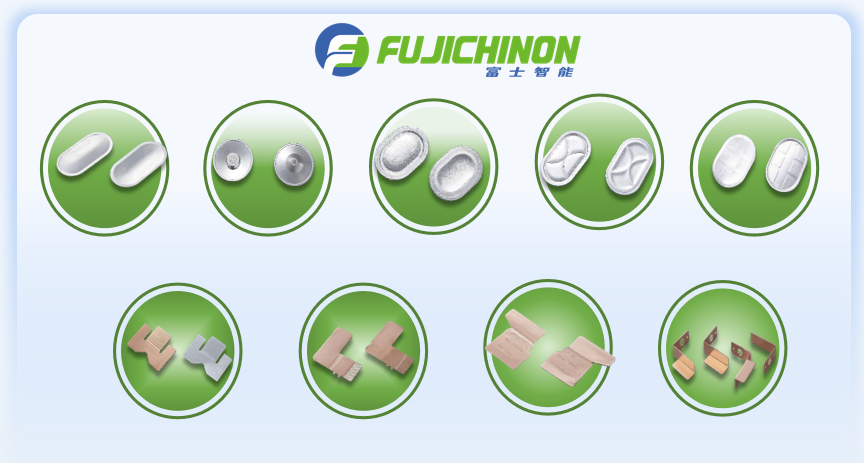
Battery cell structural components
The explosion-proof valve is the only indispensable safety component in the battery cell structure, specifically used for the top covers of new energy vehicle battery cells and new energy storage battery cells. It ensures timely and effective pressure relief by opening the valve when the internal pressure of the cell abnormally rises above the rated tolerance pressure. Its key characteristics are crucial for ensuring the safety of the battery pack.
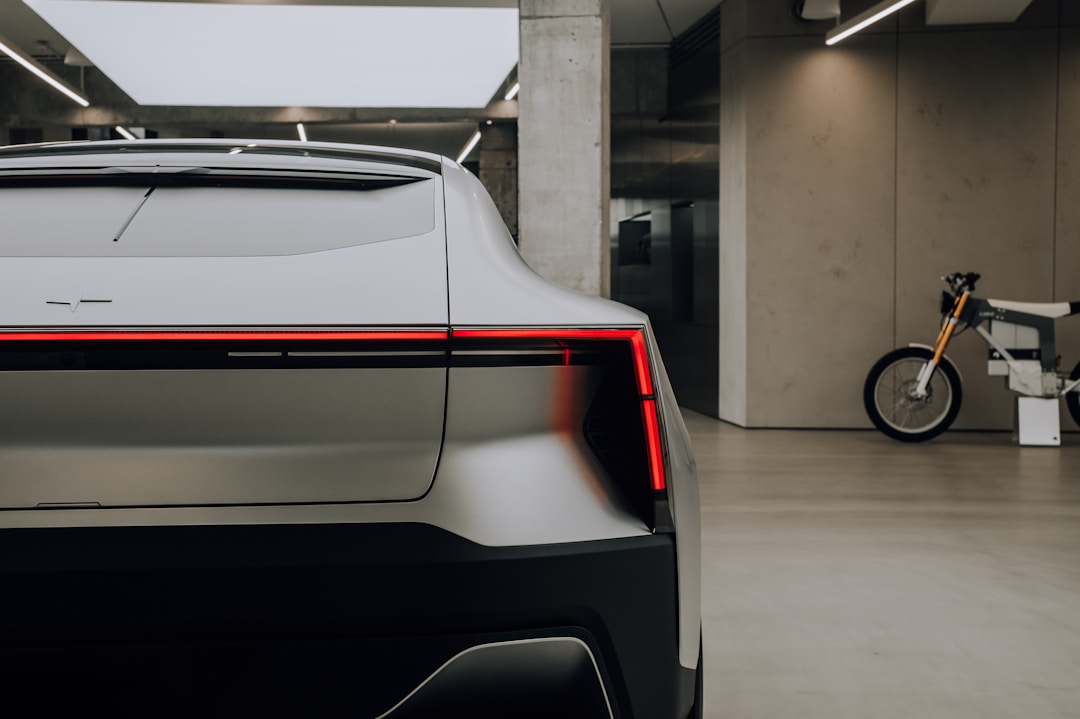
Battery tray profiles, as an indispensable key component of new energy vehicles, are the main structural components of the structural skeleton and protective shell of lithium-ion battery packs. They are mainly used in battery pack housings, battery trays, and lightweight anti-collision beams. Aluminum alloy materials, due to their lightweight, high-strength, and corrosion-resistant properties, have become the mainstream choice for battery tray profiles, helping to improve the overall performance and cruising range of new energy vehicles. This product provides a safe protective shell and structural support for the new energy vehicle battery system module, has a heat dissipation function, provides a safe and stable operating environment for the battery system, and plays a vital role.
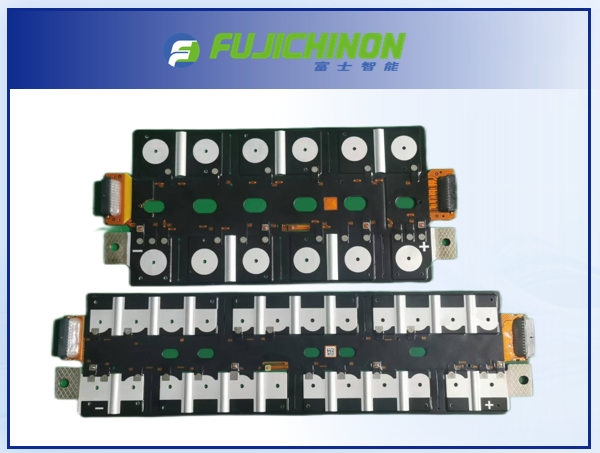
Other precision structural components for automobiles
As an electrical connection component assembled inside the battery module, it realizes the series and parallel connection between battery cells, the transmission of high voltage and large current, the acquisition and transmission of temperature signals, and the acquisition and transmission of voltage signals. The product features a lightweight and thin structure with high integration, which helps improve battery pack assembly efficiency and space utilization. It also offers advantages such as convenient customer installation and strong commonality.
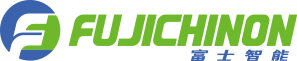
TEL
/
/
ADD
/
Address: No. 3, Xinqing 6th Road, Xinqing Science and Technology Industrial Park, Doumen, Zhuhai
Copyright © Zhuhai Fuji chinon Co., Ltd 粤ICP备2022120036号 SEO Powered by 300.cn